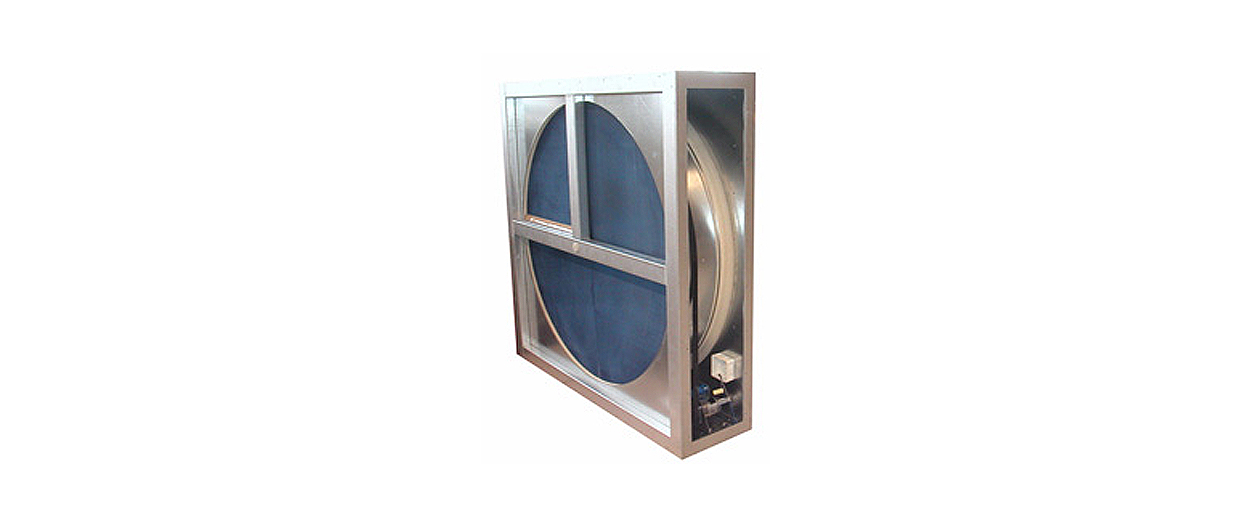
Desiccant rotors units that can be integrated into an air treatment system
Desiccant rotor for dehumidification
In most of the world, atmospheric humidity throws up challenges of different kinds to homeowners and businesses. In the manufacturing sector, companies that work with foodstuffs, pharmaceuticals, chemicals, batteries, electronic components and more need to try to find solutions to levels of relative humidity on their premises that can cause disruption at different stages of the production process. The desiccant rotor, or to be more specific, desiccant silica gel rotors, are such a technical solution. The Dessica Silica Gel rotors are designed to be used in most environments for dehumidification applications with high performance and long life.
Why desiccant rotor is the best solution to your humidity issues
Improving ventilation is one obvious way of drying out a premises. However, the effectiveness of this approach depends largely on weather conditions outside Indeed, improving an outside airflow in the premises can for example:
- In winter: decrease the relative humidity by blowing more dryer air but it will also add a calorific power consumption because the air is most likely colder than the premises atmosphere.
- In summer: The atmosphere in the premises should be colder than the outside so upgrading the outside airflow will increase relative humidity (since hotter air can contain more absolute humidity) and add the need to cool down the atmosphere which mean adding frigorific consumption.
Those two scenario are few among many other case which will worsen the premises humidity and adding temperature control issues – not something we have much control over!
Alternatively, we can heat premises to lower relative humidity. However, this has no impact on absolute humidity and the dew point. As explain previously the more the air is hot the more water it can contain. So by rising the temperature the relative humidity will decrease but the absolute humidity will remain the same. Increasing the temperature imply increasing power consumption which is also expensive.
The desiccant rotor : at the heart of dehumidification
There are various kinds of dehumidification and humidity control technologies in use today, one of which is the desiccant wheel or rotor. DESSICA systems uses two independent and countercurrent air flows through the desiccant rotor. Desiccant rotor work by directing process air through the wheel itself, which contains silica gel, a very effective adsorbent. Most of this process air is dry after having passed through the dehumidification rotor. Some air retains a little more moisture. This air is then heated (to very high temperatures of between 100 and 160°C) and sent back through the rotor again. This helps dry out the silica gel, with moisture contained in the gel evaporating into the hot air flow. The warm, but moist air is then removed, and the silica gel is ready for another process air. This second flow of air through the desiccant rotor which heat wheel is called the reactivation airflow. This airflow also has another major role : it helps clean the rotor of any contaminants thank to the decontamination capacities of high temperature – this is particularly important for the food processing, agri-food and pharmaceutical industries.
The key advantages of the desiccant wheel over other kinds of humidity control
The desiccant wheel is just one way of removing moisture. Ventilation, heating and cooling are three other approaches to dehumidification. However, each of these come with their own challenges. Ventilation requires air of a low moisture content to start off with, meaning that changing weather conditions can create all sorts of problems.
Heating, meanwhile, has no impact on absolute humidity, and is also expensive. Dessica has been working on new technologies to reduce the running costs of its systems, whilst desiccant rotors are also renowned for their long operational lifespan.
Lastly, cooling is a relatively inefficient way of removing moisture in environments where the ambient temperature is 10°C or less. Cooling-based dehumidification systems, which are ozone-depleting, making the desiccant wheel a more environmentally-friendly choice.
Remove humidity with Desiccant evaporative cooling systems
However, there are alternatives to desiccant rotor dehumidifiers, so it’s worth taking a look at precisely why these are not generally as effective. Indeed, Dessica Silica Gel rotors are also suitable for use in Desiccant Evaporative Cooling systems. The process makes it possible to closely tailor the amount and characteristics of the Silica Gel in the rotor.
This method is inefficient when the ambient temperature is under 10°C, because you need either cold water which mean above 0°C to be sure that it will not turn to ice, either frigorific fluid to go lower but take the risk to turn into ice the water from the air. Frigorific fluids are also less environmentally-friendly because it involves the use of HCFCs and this method is more maintenance-heavy mainly due to freezing issues. This alternative is actually a good combination with a desiccant rotor dehumidifier because it can cool down the air and the absolute humidity by condensation and the desiccant rotor will also decrease the absolute humidity and increase the temperature so it will decrease the relative humidity even more efficiently.
The capacity, pressure drop and other characteristics of the Dessica Silica Gel rotors can easily be calculated in our software program.
Desiccant rotor applications – let your imagination run wild!
There are an enormous number of applications for desiccant rotor dehumidifiers. Many of these relate to the food processing and associated industries, including industrial bakeries. However, there are plenty of other fields where a desiccant rotor can help out. One of these is the protection of valuable artefacts in museums, art galleries, libraries and archives. These range from old books and costumes to upholstery and even classic cars! Ice rinks also use this kind of technology to ward off fog, puddles and musty odours. Another unusual area where a desiccant rotor of the DESSICA silica gel rotors type could potentially help out is with seed storage & preservation, where germination is public enemy number one.
Dessica silica gel rotors composition
Material Composition: The rotor has a very high, 82%, active SilicaGel content and only 16% glass fibre content, the remaining 2 % is the Acrylic surface coating.
Fire resistance: The rotor has been tested according to ASTME test E-84 and achieved a flame index of 0 and a smoke produced of 0.
Technical properties: There is no limit for how high relative humidity the rotor can stand as long as droplets are not introduced into the rotor during operation. The rotor can be washed in water with weak non-alkaline detergent, after saturation in humid air.
Physical properties: The density of dry material is approx. 240 kg/m3. The media can pick up approx. 40% of it’s dry weight as moisture in humid environment. The surface compression strength of the rotor is more than 200 kPa.
On request DESSICA produce replacement rotors in sizes to fit most existing dehumidifiers.
Air dryers that can be integrated into an air treatment system
Integrable air dryers are housed in a double-wall unit with 50 mm of thermal insulation. They include the desiccant rotor and its drive system as well as the four intake and outlet connections for the intake air regeneration circuits.
Modules with desiccant rotor in a frame for mounting in an air treatment unit
The modules include a high-performance or hygienic silica gel desiccant rotor, gaskets and a drive system. They exist in a 180°/180° version for DESICCANT EVAPORATIVE COOLING applications.
Operating principle Desiccant rotors units
The process air contain humidity, pass through the process sector (blue) and comes out dry. At the same time, reactivation air heated from 100 to 165°C passes through the reactivation sector (red) and evapored moisture trapped in the desiccant rotor. With the wheel rotation, the production of dry air is continuous.
Benefits of Desiccant rotors units
Integrable into an air treatment system
- High performance desiccant rotor
- Fixed or variable speed drive
- Two configurations : 180/180° et 270/90°
- Available in painted or stainless steel version
Installations for Rotor units that can be integrated into an air treatment system
The frame desiccant rotor is intended for installation in air handling system. The installation guidelines are the follows :
- The desiccant rotor is crossed by filtered air (minimum G4).
- The seal around the frame and between the two air flows must be ensured. It is necessary to respect a maximum pressure differential between the two air flows in order to maintain a tightness (consult us).
- To ensure annual maintenance, access must be provided in order to inspect the peripheral and radial seals, the gear motor, the bearings and the rotor axle.
Dimensions of standards design, possibility to get a tailor-made rotor
For large diameters, the rotor is delivered in sectors, the frame in 2 parts and the whole is assembled on site.
Applications
Discover our products and solutions in application